Plastic Injection Molding Case Studies
Business Activities That May Qualify
- Designing, prototyping, fabricating and/or testing mold and tooling
- Engineering and process development
- Applying material application study
- Conducting emperature study
- Studying injection time analysis
- Performing a gate seal study
- Conducting a cavity balance assessment
- Performing a rack and hold pressure study
- Conducting first article test runs by engineers, tool makers, production supervisors, and operators
- Ensuring quality assurance, including inspecting testing of the parts produced including dimension checks, visual inspections, non-destructive testing, leak testing, and other part specific tests
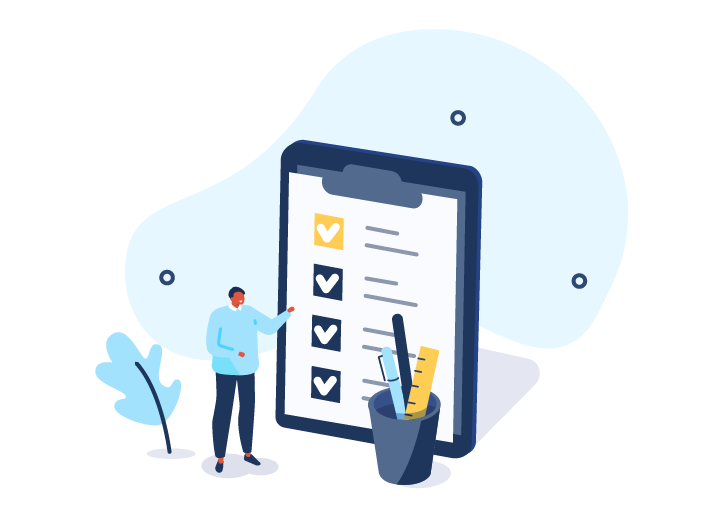
Here Are Some of Our Clients' Success Stories:
Plastic Injection Molding Company
$32,000
R&D Tax Credits Realized
Annual Revenue: $1.5 MM
Plastic Injection Molding Company
$75,000
R&D Tax Credits Realized
Annual Revenue: $4 MM
Plastic Injection Molding Company
$192,000
R&D Tax Credits Realized
Annual Revenue: $35 MM
Calculate Your R&D Tax Credit
In 2021 alone, alliantgroup delivered over $2.3 billion in credits and incentives to over 14,000 businesses. And we do not want to stop here without helping you. Let our experts research and provide information that you need to understand how this credit can genuinely benefit your business.
Take our short quiz to get an idea of what this benefit can look like for your business today
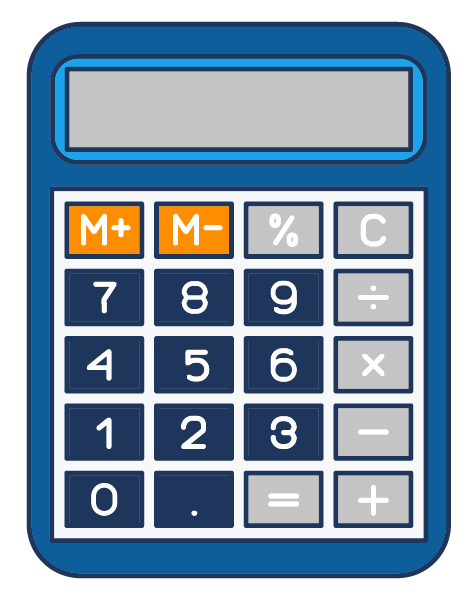